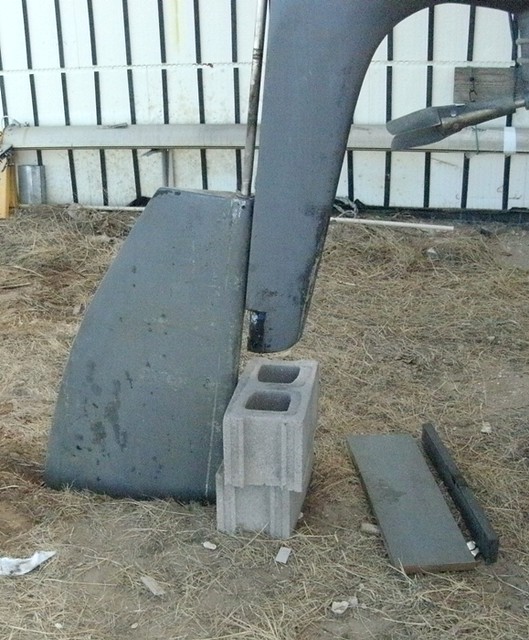
That's probably a metaphor for owning an old sailboat: you've dug yourself a deep hole, but it must get deeper still before you are finished.

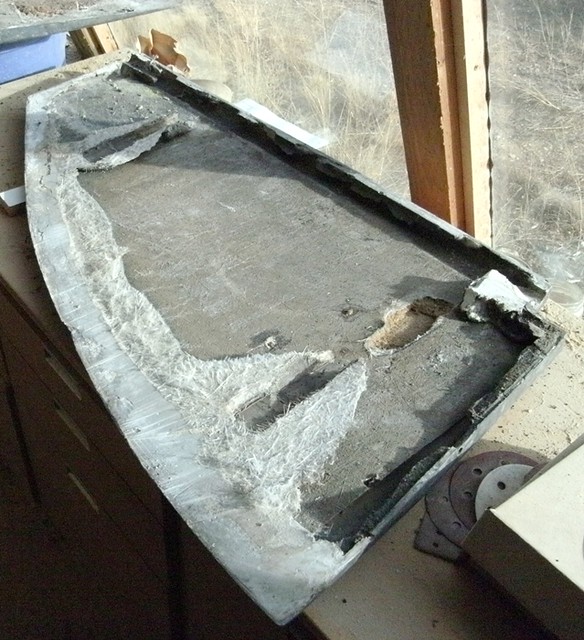
That's 3/8" foam (like CoreCell) on the inside of each rudder half, with one crude layer of matting formed over it using polyester resin. The space between the layups is mostly empty. And of course, water eventually gets in there. Our blade showed several generations of attempted fixes, including MarineTex bedding around the shaft and yellow squirt foam injected into the top of the cavity. They didn't help, much.
First stage of the cleanup: removing the inner skin and saturated foam. Again, a multitool is the business for controlled destruction.
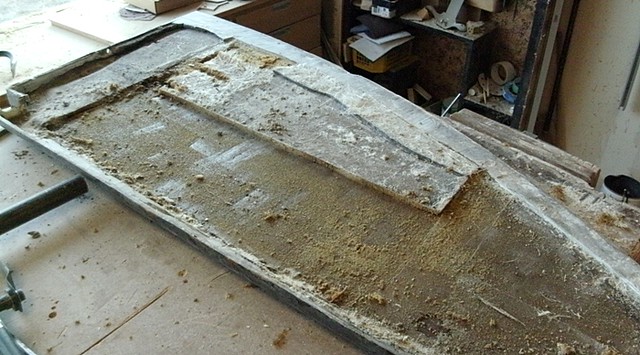
We plan to scrape it to raw laminate, then give the shell a couple weeks in the sun to drive all the water out of it. Then I will start rebuilding it. Plan is a layer of 4oz fabric epoxied to the inside face; then build up bedding for the stock (we will weld on three more flanges); then fill each half with expanding closed-cell foam & shave it flush; then epoxy the two halves together. The whole assembly will then be ground down, skinned in 6oz cloth, faired, and painted.
Here's the stock. Needs more flanges. There are a few shallow grooves worn where the shaft has turned against various bushings; should we start with a new piece of steel, or just reuse this one?
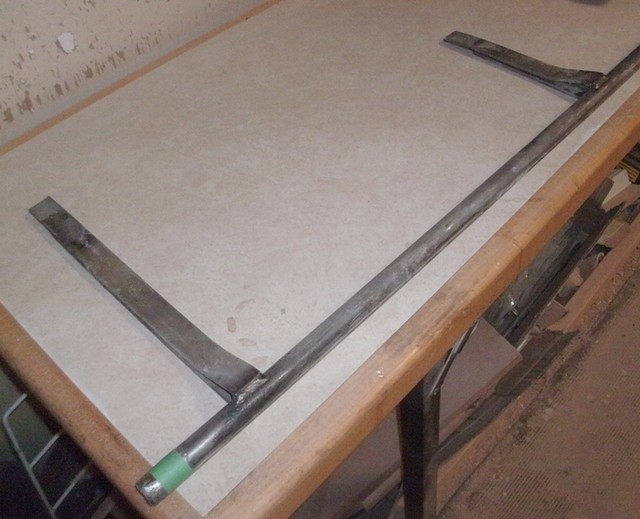